Concentrated Sulfuric Acid (H2SO4) 93%-98%
The use of concentrated sulfuric acid for pH control in water and wastewater treatment, agriculture, bio-energy and chemical processes is often the best choice due to the ready availability, low cost and effectiveness of this acid.
Handling and Injection of the acid requires some special considerations.
Injection
Concentrated sulfuric acid (93%-98%) is an oily liquid with a density nearly twice that of water and a viscosity similar to honey. Sulfuric acid typically requires additional diffusion or mixing techniques to assure reliable diffusion into the process stream without damage to the process piping.
If at all possible, it is best to predilute the acid down to 0.5%-3% concentration. (Acid dilution is discussed at the bottom of this page).
Advantages of injecting a weaker acid include:
-
A weaker acid stream is much more miscible and easier to diffuse into a water stream.
-
The likelihood of corrosion to the pipeline is lessened.
-
Greater volume allows for higher velocities and a larger injection plume at the injector to improve distribution.
-
Better control over final pH as the larger flow volume is easier to control.
-
Temperature rise of 0.5%-3% dilute acid due to the heat of reaction of the acid with water is much lower, and allows for easier handling with common piping materials. This can eliminate PTFE lined steel piping which is recommended for concentrated acid dilution systems.
-
During system shutdown, the acid that remains in the quill with mix with the water, and will not settle at the bottom of the piping in a corrosive, viscous puddle.
If small amounts of concentrated acid are to be injected directly into the water stream we recommend the following techniques:
-
Ensure that the main pipeline water velocity is high to ensure turbulent flow for good mixing and a minimum of hot spots (typically above 4 ft/sec).
-
Consider a sparger constructed of PTFE (Teflon) or a sparger having a PTFE liner. Only PTFE (or similar fluoropolymers such as PFA) is resistant to the wide range of acid concentrations that are possible at or near the injection point.
-
Use a multi-orifice sparger sized for high velocities at the orifice holes to assure rapid distribution of the acid.
-
Consider the use of a multi-orifice injector/mixing tee system, venturi eductor, or static mixer at the injection point.
-
If possible, use a piping that has some resistance to sulfuric acid, such as PVC, CPVC or epoxy coated or fiberglass lined steel pipe acid for approximately 20 pipe diameters downstream and 3 pipe diameters upstream of the injection point. 316L SS also can be used, however the longitudinal welded seam can often be preferentially attacked by the acid, and should be installed at the top of the pipe or have a epoxy coating such as Scotchkote or Tnemec Pota pox applied to the seam.
-
Ensure that the control logic of the acid injection will absolutely not allow acid to be injected into the pipeline if the water flow should be stopped or slowed for any reason. Typically this requires a flow switch or sensor.
-
If the system is subject to frequent shutdown, use a injection quill with a minimum interior volume so that only small amounts of concentrated acid remain in the piping after shutdown. This will reduce the possibility of pooling of the acid at the bottom of the piping.
-
Use check valves close to the injection point to ensure that water does not enter the concentrated acid piping. Some designers use dual check valves or a temperature switch for detection of check valve failure on the piping to ensure that there is no water intrusion at this point.
Materials
Care must be taken when choosing materials for diffusers or injectors that can withstand sulfuric acid across during dilution process.
Polymers
PVC
PVC (Schedule 80 Type 1 -Gray) is a good low cost material that can chemically withstand all concentrations of sulfuric acid. PVC has relatively low temperature resistance (a maximum working temperature of 140 ºF), and should not be used for the diffuser components such as the injector or quill that are near the dilution or diffusion of the acid, as the heat of reaction can damage the pipe.
CPVC
CPVC (Schedule 80 Type 1 -Gray) is a good low cost material that can also withstand all concentrations of sulfuric acid. With a maximum service temperature of 200 ºF, CPVC can withstand some heat of dilution, for injectors or diffusers that are adding small amounts of acid..
Kynar (polyvinylediene fluoride)
Has excellent resistance for all acid concentrations up to 93%. With a higher working temperature of up to 225 ºF, it can make an excellent choice for many dilution or chemical diffusion projects. It is not recommended for 98% sulfuric acid as it will exhibit some degradation over time.
PTFE/ Teflon
The only material that can withstand all concentrations of sulfuric acid at the temperatures that can be created during the dilution of sulfuric acid is PTFE (Teflon) or other fluoropolymers such as PFA. The best piping material is a Teflon lined steel piping system which has a maximum working temperature of about 350°F. This material is expensive, and may not be needed in many cases. Additionally, the lengths of pipe cannot be made too long, and there may be many flanged piping connections. Inyo Process can supply Teflon quills can be supplied in a variety of styles, including all Teflon and Teflon lined Hastelloy or FRP wrapped Teflon for added stiffness.
CTFE/ Halar
Can be used for sulfuric acid. Has a lower maximum temperature (approximately 250°F) than teflon, and is typically more expensive, with limited shapes and pipe fitting available. Can be welded, however it will discolor to a brown or yellow when used with concentrated sulfuric acid.
Epoxy Resin Fiberglass
Epoxy Resin Fiberglass has good resistance to sulfuric acid. As an example, Hetron 922, which is often used in potable water systems is resistance to 70% sulfuric acid up to about 180 ºF. Like many polymers, care must be taken to ensure that concentrated acid is not spilled on the fiberglass in the piping, as the spot temperatures will degrade the epoxy and cause failure.
Metals
Carbon Steel
Carbon Steel is often found in the piping of concentrated sulfuric acid. It is not recommended or discussed in detail, as it will quickly degrade in the presence of acid and water.
Stainless Steel
Stainless Steel has some resistance to sulfuric acid. 316L S.S. often is used as piping material around the quill (never use stainless steel for the quill) with good success.
Choosing an appropriate type of stainless steel or predicting the resistance or life-span of stainless steel material is beyond the scope of this web article. We will discuss only two alloys, Alloy 20 & Hastelloy C-276
Alloy 20
Alloy 20 (20Cb-3) is one of the so-called "Super" stainless steels that was designed for maximum resistance to acid attack. It's nickel, chromium, molybdenum and copper content contribute to its overall resistance to chloride stress corrosion cracking and general pitting attack. The alloy is stabilized with columbium to minimize carbide precipitation during welding. It has good mechanical properties and can be fabricated with comparative ease. Corrosion can occur on a Alloy 20 quill if concentrated sulfuric acid is allowed to react with the water and reach the high temperatures of approximately 150ºF, particularly if the concentration even temporarily reaches the 30-80% region, which can easily occur. Due to the metal material, longer quills can be supplied compared to teflon without bending or breaking. Click on the isocorrosion graph for more information.
Hastelloy C-276
Hastelloy C-276 is a good choice for nearly all concentrations of sulfuric acid as long as temperatures are managed. At higher temperatures, corrosion rates will likely be unacceptable. Corrosion can occur on a Hastelloy quill if concentrated sulfuric acid is allowed to react with the water and reach the high temperatures of approximately 150ºF, particularly if the concentration even temporarily reaches the 30-80% region, which can easily occur. Click on the isocorrosion graph for more information.
Titanium
Not recommended, as the corrosion rates are too high.
Tantalum, platinum, gold & zirconium
Tantalum, platinum, gold & zirconium have good resistance to sulfuric acid. They will not be discussed in detail, as these exotic metals are typically cost prohibitive for all but the most demanding high temperature applications.
Ceramics
There are a number of ceramics and glass that also exhibit good resistance to sulfuric acid particularly at elevated temperatures. They too will not be discussed in detail, as there are few components that are commercially available for chemical diffusion.
Elastomers
Use Viton or Teflon for gaskets or flexible material.
Chart of Sulfuric Acid Specific Gravities & Weights at Different Concentrations
Chart of Specific Gravities & Weights of Various Concentrations of Sulfuric Acid
Dilution of Sulfuric Acid
Concentrated sulfuric acid has a strong affinity for water and will react violent and generate heat when coming into contact with water. Always add acid to the water when diluting sulfuric acid. A large amount of heat may be released, and could cause burns.
Below is a chart that details some typical dilutions of sulfuric acid and the heat of enthalpy that is produced.
Acid can be diluted two ways:
Calculating Dilution Quantities
The RECTANGLE METHOD is an easy method of determining the amounts of acid and water or other fluid to dilute sulfuric acid.
EXAMPLE:
To determine how many pounds of water it takes to dilute 93% sulfuric acid to create 100 pounds of 1% acid.
A rectangle is drawn with the desired strength in the center and the original solution strength on the left-hand side. By subtracting the smaller number from the larger number along the diagonal, the answer appears on the right-hand side as shown.
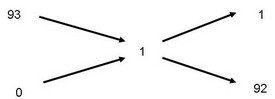
Therefore 1 lb of 93% acid (upper right corner) and 92 lb of dilution water(lower right corner) is needed to produce 93 lbs (sum of water and acid weights) of 1% acid solution.
To convert this to an even 100 lbs of 1% acid, multiply each of these by 100/93 or 1.075
Therefore, 1.075 x 1 lb. of 93% acid = 1.075 lb of 93% acid
&
1.075 x 92 lb. of water = 98.9 lb. of water
Will produce 100 lbs. of 1% acid
To convert this to volume (gallons), divide the weight by it’s specific gravity & divide by the specific weight of water (8.34 lbs/gal at 60ºF):
1.075 lb acid / (1.84 x 8.34 lbs/gal) = 0.07 gal of 93% acid
Mixed with
98.9 lb water / (1.0 x 8.34 lbs/gal) = 11.85 gal of water
Will create 1% acid
(A ratio of 169:1)